What is quality improvement methodology?
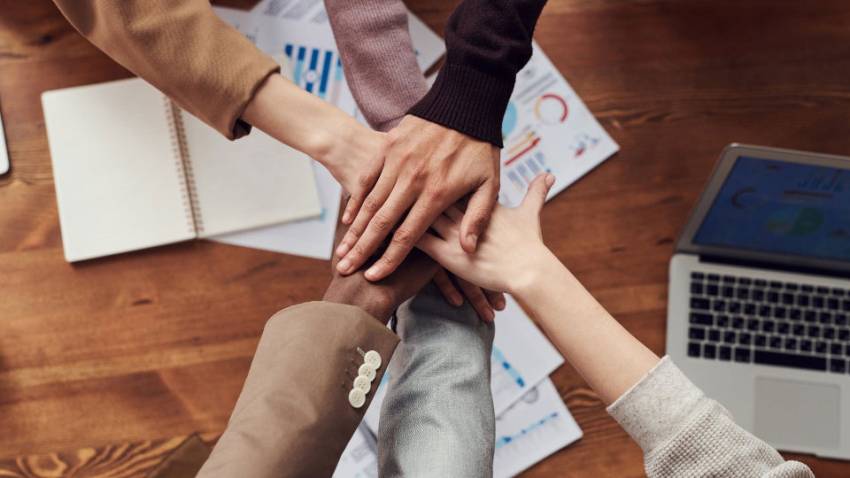
New Delhi : Whenever a company faces any issue, they must find the root cause of the problem. If they fail in doing so, they might never come out of debt. If the organization wants to uncover the root cause of the problem, determine the best path to gain profits, and meet the deadlines, all the owners/ founders/ CEO of the company must understand what quality improvement methodology is. Along with the basics of it, they need to understand the importance of quality improvement in the process of developing a successful business.
If someone asks us to define quality improvement, then we will set it as,
“A process of taking an entity from nothing to something, from good to better, and from better to best. It creates the environment of positivity to take an entity towards the defined goals of success.”
Once we identify the need for quality improvement, we use the formal process to identify the root cause. And if the root cause of the problem is identified, solving the problem will not be a big issue.
The below-mentioned steps help you to build a culture of finding the root cause and defining the solution. Along with a solution, your team will be ready to create an action plan to reach the set goals.
Steps to find the solution for a problem
1) List and prioritize the improvement opportunities after finding the root cause of the problem.
Audits, accounting, and many other steps might help you find the root cause of the problem. Knowing the difficulties, the team may now prioritize on documenting the root cause of the problem. So that if the same thing happens in the future, the future team may react accordingly.
Once the problem is realized, the team can plan to change the method of reaching the defined goals so that the same problem doesn’t occur again. There are many other improvements that the organization may decide after finding the issues.
2) Define the essential objectives of improvement
Once you know that there are chances of improving the methodology of gaining profits, the team must define the crucial objectives of improvement. These objectives will state the necessity of creating an action plan to achieve the identified goals.
3) Define the requirements
Once you know the objectives of improvement, you need to find your process requirements to reach the destined goals. The requirement list will work as a raw material for you to gain the necessary profits at the end of the action plan.
4) Collect and organize data
Once the requirement is finalized, the team needs to start finding the required data to help the organization in every way. The team needs to go through every discipline of the work so that nothing remains unchecked while solving the problems.
5) Generate potential solutions
Years of experience help a team define the best solution for the problem that occurred when creating a successful business. Experts having lean six sigma green belt certification can help you decide the best solutions for the problem that brought a pause in your route towards success.
6) Select the best solution
Again this step can be a little tricky. It is easy to list solutions for a problem. But, it is not easy to select the best among the plethora of solutions. We might ask a lean six sigma green belt certified expert to help find the best solution. If we fail to do so at this instance, it might bring us back to the same position where we have to start again from the bottom.
7) Implement the solution and evaluate the result
A lean six sigma green belt certified associate may decide on the best solution to solve the problem. But then the team has to follow every single step defined in order to resolve the issue. In the process, they might fail or miss at any point. But as a team, you all need to be very careful while following the steps mentioned in the solution.
Also, the team needs to monitor whether, after each step, the defined results are met or not. If not, then they need to find the solution for the unsatisfied result.
It is a multi-step procedure that leads to the final results.
8) Continue to track
You cannot find success in one day. You need to keep your trial and error continuing until you find success in your business. Keep the tracking game on until the final results are met. A successful business is not a one-day match; it is a test match. It may lead to success, draw (no results), or loss. But it keeps your enthusiasm at the top.
Once you receive success in your solutions, it does not mean you need to stop tracking your business's success. It would help if you kept on following to find new methods and tricks to reach the destined results.
It becomes easy for you to define the root cause, set the new goals, list the solutions, find the best solution of the list, implement the resolution, and keep an eye on the implementation if you have an expert who has experience in each of these steps we mentioned above. By expert, we meant a lean six sigma green belt certified associate.
Problems will never come to an end, but finding a solution will always be tricky. Considering the amount of competition, the present world has, and the future world may have, we feel the requirement of having an expert with lean six sigma green belt certification will rise day by day. You may find it as if we are marketing about the experts, but our industrial experience led us to mention these experts.
Also, these experts are the only medium to ensure that the steps we defined above are maintained and run in the required manner. The experience these experts carry with their resume in hand establishes their requirements in the market. It has been in the boom, and it will remain at the top in the coming years for sure.